RANGER, in the framework of its development plan of innovative technologies, has conceived the first formulation of BMC and SMC from renewable sources. For this formulation, bio-resins were used, strengthened by natural-source fibers such as flax and hemp. Bio-resins are resins that derive some or all of their constituent monomers from biological sources and are increasingly replacing monomers traditionally derived from petrochemicals.
Some interesting considerations came out of the testing phase specifically related to the way the productive plants need to be modified and/or updated at the level of production of the semi-finished product. These upgrades shall likewise affect the mold and the press to be utilized during production.
Let’s see them.
The SMC line production used had a floor width of 800 mm, to whom a cutting group was added along with a dispersion of the fibers to ensure better distribution. Furthermore, heating rollers were turned on at the end of the line to get a better permeation. These testing activities allowed the development of technical skills for the treatment of natural fibers in a continuous production process, linked, in particular, with protection from humidity and reaction during the compaction phase.
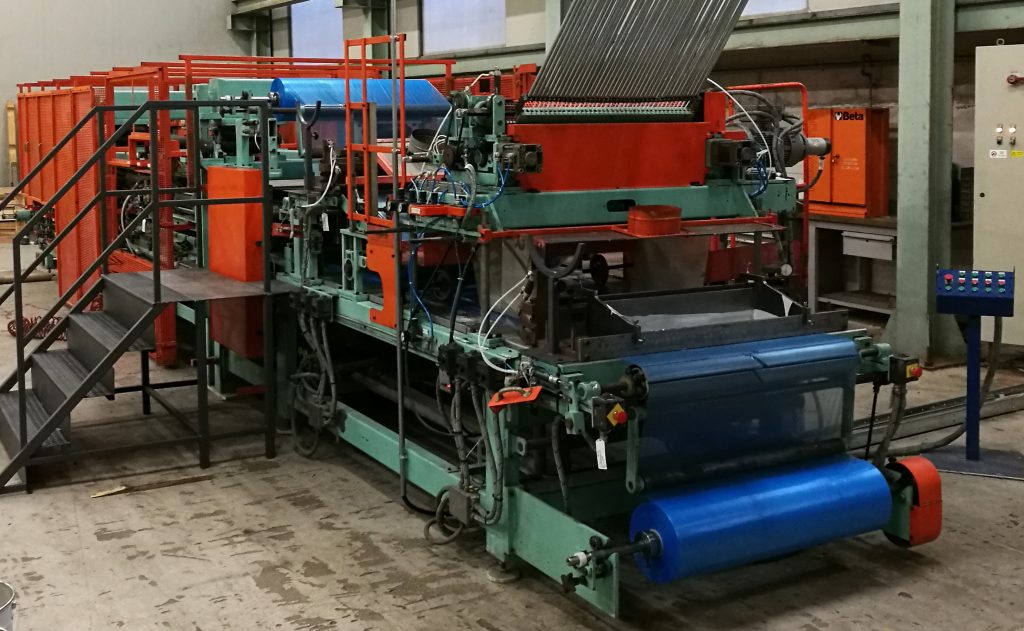
SMC LINE
With regards to the moulding material, RANGER longstanding experience as mould makers and moulder allowed to proceed with some key interventions on the mould, namely the thermic treatment and the division line, both pivotal to the achievement of the objective. Even the compression press used in the process had to be adjusted specifically concerning the closing phase.
The outcome of these testing resulted in the making of samples of that will be presented to the upcoming JEC 2020 at the Ranger stand P82 Hall 5.
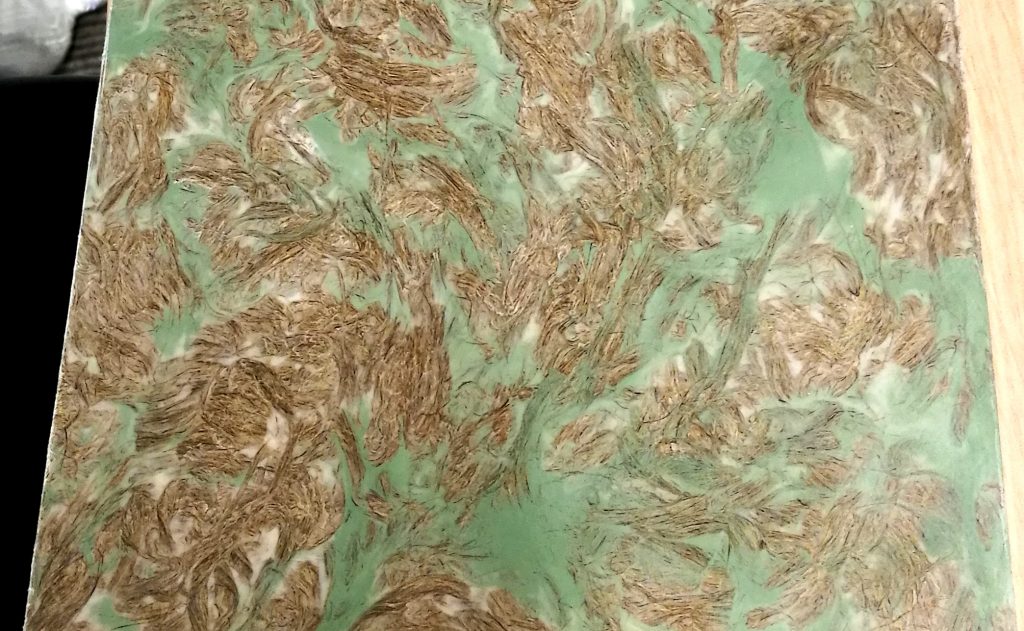
GMC®
While the technical specifics of these materials are still to be fully characterized, what is by now evident is the wide range of solutions that can be developed for countless industrial and commercial applications with remarkable benefits for the environment and sustainability.
RANGER’s first target is the successful replacement of the traditional SMC with the GMC® for electric panels. To this end, a specific formulation that can meet current regulations is under development in collaboration with a specialized partner in the field.
The second application on which RANGER is working is the use of these materials in the automotive industry with regard to the production of the battery pack and, more specifically, for the lid. For the latter, the company filed an application for a patent to protect the cabin from electromagnetic waves by inserting an additional component into the production process which will be also showcased during the next JEC 2020.
But the real target of these technologies is their applications in the building industry increasingly looking for eco-friendly solutions. RANGER is currently filing several patents for the use of this type of material and is seeking partnerships with companies interested in further developing technologies for new applications to be presented to the market.
RANGER has currently two hubs in Lombardy for production and research. The one in Carate Brianza is a development centre composed of a line of SMC and one of BMC, plus a laboratory press. The other site, located in Castelletto Cervo, is dedicated to the research and development of composites materials and lightweight solutions especially for EV cars and other structural applications. This site, opened in 2010, has been recently enlarged with a new department, conceived and designated to accommodate up to 4,000-tons press with plate dimensions designed to print any type of composite product.
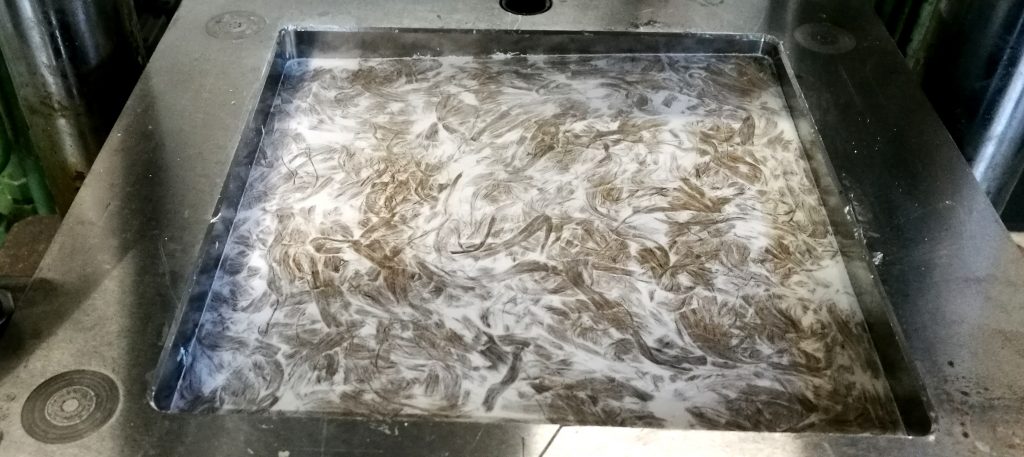
GMC® MOULDING LAB
With the development of the GMC®, the company not only reaffirms its know-how and penchant for innovation but also its ability to detect and respond to the increased demand from consumers and end-users for sustainable and environmentally friendly solutions.